Sep 26 2014
A new step is being taken in the development of ultra-stable sensors of small forces. EPFL researchers have found a way to eradicate external perturbations from interfering with their state-of-the art optomechanical measurement systems.
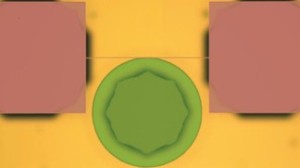
Last year, Tobias Kippenberg and his team from the Laboratory of Photonics and Quantum Measurements (LPQM1) presented a new-generation sensor capable of detecting very small forces with unprecedented efficiency. These devices, developed and fabricated at the Center of MicroNanofabrication (CMi) at EPFL have already opened new frontiers in both applied and fundamental science.
However the potential of these systems, called nanomechanical oscillators, is affected by their increased sensitivity to external perturbations. So far some "noises", due to temperature variations for instance, have prevented the device from working perfectly. These imperfections might now soon disappear.
EPFL scientists Emanuel Gavartin, Pierre Verlot and Tobias Kippenberg have recently managed to isolate and eliminate external "noises" that deteriorate the performance of the sensors. Their discovery paves the way to the development of some of the best sensors in the world. Their results have been published in Nature Communications.
A microscopic vibrating string
This is how it works: nanomechanical oscillators are composed of a string a few hundred nanometers thick, that can be actuated by applying a known external force. Such a device can then be used to detect very small particles, e.g. single molecules, which arrive on its surface. Depending on its property, each molecule changes the string vibration in a specific way. These changes act as a molecule's "signature", allowing researchers to know what kind of molecule is present in a specific area, even in a very small quantity.
A laser to read the vibrations
In order to read the changes in the string vibration, the scientists normally direct a laser into a round glass cavity located under the string. The laser beam spins several ten thousand times around the disk for a few nanoseconds, and finally gets out. During the spin, the beam undergoes changes depending on the string's vibration. By analyzing the frequency changes in the laser before and after the spin, researchers can therefore find out everything that happened at the string surface.
The problem now is that this extraordinary sensors are not only sensitive towards signals or forces one seeks to detect, but also towards external noise sources resulting from different phenomena such as temperature variations in a room, or chemical processes occurring at the device's surface.
Two types of noises
In reality, nanomechanical oscillators suffer from two kinds of perturbation. First of all, the device is subject to a natural imprecision governed by fundamental physics that affects all oscillators. The second kind of perturbations is caused by external changes in the environment. "Until now the internal perturbations had never affected the measurement in a significant way," Emanuel Gavartin comments. "We were more concerned about the noises coming from the surroundings of the oscillator, as they have a much larger impact on the oscillator system."
An oscillation in several directions
To get rid of the external frequency fluctuations, the scientists relied on a simple fact. When it vibrates like the string of a guitar, the microscopic string simultaneously oscillates up and down and left and right, as well as in several other directions. Just like an oscillating guitar string with several overtones.
EPFL scientists observed that when external noises perturb the device - a rise of temperature, for instance - there was a correlation between the changes occurring in the up and down mode, and in the left and right mode. In other words, they found out that each oscillation mode responded similarly to an identical external perturbation.
Given this phenomenon, they used one mode to detect the external noise perturbation and then derived a correction to remove the external noise from the other mode to be used for sensing applications. The results were really convincing, as they allowed a nearly total removal of external noise. "When such a perturbation occurs, we proceed very quickly to the analysis of the variations of the oscillation mode," explains Emanuel Gavartin. "Then, we apply a laser to counteract the fluctuation and stabilize the device."
A very efficient stabilization
The new method will allow developing almost perfect ultra-efficient sensors, with an impact in both fundamental and applied studies. Thanks to the presence of different modes, the noise correction does not affect the detection capabilities of the 'sensing mode'. "Our technique is very promising for the detection of very small masses. Further applications lie in fundamental science, as low-noise mechanical oscillators pave the way to state-of-the-art experiments in quantum physics", says Emanuel Gavartin.
More information: Stabilization of a linear nanomechanical oscillator to its thermodynamic limit